一、CNC 原理與系統架構
數位化設計與刀路生成
CAD 建模:在 SolidWorks、Fusion 360 等軟體中,以參數化方式建立零件模型,並做好特徵標註(孔、槽、曲面)。
CAM 刀路規劃:設定毛坯尺寸、對刀點(工件坐標系原點)、選擇刀具、指定粗加工與精加工策略。採用等高切削(Z‑Level)、三維並行銑(3D Parallel)或螺旋入刀(Spiral Entry)等演算法,並在模擬中檢查干涉與殘留料。
G‑code 與控制器
後處理器(Post‑Processor):將 CAM 生成的刀路轉換為符合 Fanuc、Siemens、Heidenhain 等控制器語法的 G‑code。
插補運動:控制器解析 G0/G1(快速與線性進給)、G2/G3(圓弧進給)等指令,透過軸向插補演算法產生平滑軌跡。
閉環回饋:搭配光柵尺、線性電位計或旋轉編碼器,實現位置與速度的實時校正,確保定位精度可達 ±0.005 mm。
機床硬體要素
床身與滑軌:優先選擇高剛性鑄鐵或樹脂砂模床身,搭配直線導軌或滾珠螺桿,以減少熱變形與振動。
主軸系統:視材料與工序需求,可選擇 3 000–15 000 RPM 的高速主軸,或具高扭矩、低轉速特性的重載主軸。
伺服驅動:閉環伺服馬達搭配高分辨率編碼器(至少 20 000 ppr),提供穩定的力矩輸出與快速響應。
二、機台類型與選型關鍵
車床 vs. 銑床 vs. 加工中心
車床:適合回轉體零件,如軸類、套筒,常見規格 Φ 300–600 mm × L 500–2 000 mm。
銑床:以刀具旋轉對工件平面切削,VMC(立式)操作直覺、HMC(臥式)排屑佳、刀庫大。
加工中心:集成車、銑、鑽、攻牙功能,刀庫可達 24–60 把,支持自動換刀與自動測量。
五軸/多軸機床
增加 A、B 旋轉軸,可任意角度切削複雜曲面,避免二次裝夾誤差。
適用航空航太、醫療器械、汽車模具等對曲面光潔度與公差要求高的領域。
選機要點
加工範圍:X、Y、Z 行程與最大負載;確認工件最大尺寸與重量。
精度規格:定位精度(±0.005 mm)、重複定位精度、表面粗糙度(Ra 0.4 μm)。
自動化程度:從手動上下料、半自動換刀到全自動機械手+AGV。
預算與售後:機台到岸價、裝機調試費用,本地維修響應時間、備件供應穩定性。
三、材料與刀具選擇
典型材料加工特性
材料 | 應用範疇 | 加工重點 |
鋁合金 | 航空散熱片、汽車零件 | 切削速度高(VC = 200–400 m/min),需強排屑與霧化冷卻 |
碳鋼/合金鋼 | 模具、結構件、刀具 | 切削溫度高,建議使用 TiAlN 塗層硬質合金刀具+充分潤滑 |
不鏽鋼 | 醫療器械、食品設備 | 熱傳導差,易黏刀,採多刃刀具+低速高進給策略 |
銅/黃銅 | 電氣散熱片、接點 | 刀具易堵屑,採用低轉速、低進給、適量冷卻 |
工程塑膠 | 功能原型、小批量 | 切削深度淺,避免過熱產生融化現象,可 用乾切或壓縮空氣排屑 |
刀具類型與磨損管理
刀具結構:立銑刀、球頭刀、螺旋銑刀、鑽頭、絲錐。
常見磨損模式:崩刃(Chipping)、磨圓(Flank Wear)、黏附磨損(Built‑Up Edge)。
刀具補償:定期以量刃儀或雷射刀具測量儀回讀刀具半徑與長度,並在控制器設定 R‑補償(G41/G42)與 L‑補償。
四、切削參數與實例計算
1.主軸轉速(RPM)
RPM=VC×1000π×DRPM = \frac{VC \times 1000}{\pi \times D}RPM=π×DVC×1000
例如:鋁件 VC = 300 m/min,D = 10 mm → RPM ≈ 300 × 1000π × 10\tfrac{300 × 1000}{π × 10}π × 10300 × 1000 ≈ 9549 rpm
2.進給速率(F)
F=fz×Z×RPMF = f_z \times Z \times RPMF=fz×Z×RPM
fzf_zfz=0.08 mm/z, Z=4 → F = 0.08×4×9549 ≈ 3055 mm/min
3.切深(Depth of Cut)
粗加工:3–5 mm,進給參數上限,快速去料。
精加工:0.2–0.5 mm,保持穩定切削力與表面品質。
完整範例:
加工一塊 100×100×20 mm 的鋁合金平面:
粗加工:D = 12 mm, VC = 280 m/min → RPM ≈ 7441 rpm, fz = 0.1 mm/z → F ≈ 0.1×4×7441 = 2976 mm/min
精加工:D = 12 mm, VC = 150 m/min → RPM ≈ 3989 rpm, fz = 0.04 mm/z → F ≈ 0.04×4×3989 = 638 mm/min
五、CAM 操作與仿真驗證
- 模型檢查:匯入 STEP/IGES,清理重疊/開洞面,確保拓樸完整。
- 工件與夾具設定:定義毛坯尺寸(留料 5–10%)、坐標系原點與方向。
- 刀路策略:選擇等高切削、三維並行銑、平面銑、鑽孔及攻牙序列。
- 碰撞檢查:在仿真中載入機台與夾具模型,全面檢測干涉。
- 後處理:選擇正確控制器格式,生成 G‑code,並在 NC‑Simulator 逐行驗證。
六、故障診斷與品質管控
1.常見故障
刀具斷裂:通常因切削參數過高、工件震動、夾具不穩。
程式碰撞:G‑code 錯誤、刀長設定錯誤、夾具干涉。
精度漂移:熱變形、絲桿間隙、閉環回饋異常。
2.排除方法
降低進給/切深,檢查夾具安裝;重新校正刀長與回饋元件;改善冷卻與切削環境。
3.品質檢測
卡尺、千分儀:快速檢測線性尺寸與孔徑公差。
三坐標測量機(CMM):高精度檢驗複雜幾何與形位公差。
粗糙度儀:測量 Ra、Rz,確保表面品質符合要求。
七、日常保養小撇步
- 切屑清理:每天下班前,用氣槍或刷子把機台、滑軌、刀庫裡的切屑清乾淨,避免鐵屑卡滯,造成走軌抖動。
- 潤滑保養:依機台保養手冊規定,每日或每週定時加注導軌、絲桿潤滑油;用對指定型號的專用油脂,避免使用機油或柴油。
- 冷卻液檢測:每週量測冷卻液濃度與 pH 值,濃度不足或雜質過多都要及時更換,保持切削效果與刀具壽命。
- 電氣櫃清潔:每月關機後打開電箱,吹走濾網與風扇上的灰塵,避免過熱或線路短路。
- 對刀儀校正:建議每月用對刀儀或雷射對刀儀做精度校驗,確保 G‑code 裡的刀長/刀徑補償值不會累積誤差。
- 備件檢視:定期檢查易損耗零件(如密封圈、風扇濾網、油封等),預留備品,不讓生產因小零件缺貨停擺。
八、 品質檢測工具
- 游標卡尺/千分尺:方便又迅速,適合量測外徑、孔徑、軸長等常規尺寸。但操作要輕柔、校正要準確,否則容易讀值偏差。
- 高度尺+鋼板基座:用來檢測平面高度差、階梯高度,搭配指示表可做到 0.01 mm 的分辨率。
- 三坐標測量機(CMM):對複雜曲面與形位公差有絕對優勢,能量測輪廓、圓柱度、平面度等高階公差。建議定期校驗探針與機台精度。
- 粗糙度測量儀:測 Ra、Rz 等表面粗糙度指標,對於需要鏡面或功能性表面(如密封面)尤其重要。
- 投影儀/輪廓儀:快速檢查零件輪廓與角度,尤其適合批量檢測同一夾治具下的零件一致性。
- 色澤對色卡/電鍍膜厚儀:對於表面處理有特殊要求的零件,如陽極、電鍍或烤漆件,可用專用儀器或對色卡做品質把關。
擁有多年鈑金加工、CNC 加工及焊接機架經驗的專業團隊,每一步從圖面評估、刀具選擇到參數優化都精準把關,確保零件公差達到 ±0.005 mm,表面品質穩定如新。與其在內部摸索、耗費時間和人力,不如把交期、品質和售後維護都交給我們,全程透明報價、快速響應,不僅節省成本,更能讓您專注核心業務,快速提升競爭力。
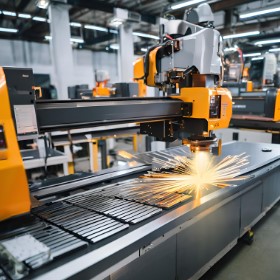